These rubidium oscillators run hot, very hot. The Rubidium lamp chamber is heated to over +106°C before ignition occurs, the resonant cavity is kept at +70°C to maintain it’s thermal stability. This means that heat needs to go somewhere, usually to the ambient if we can.
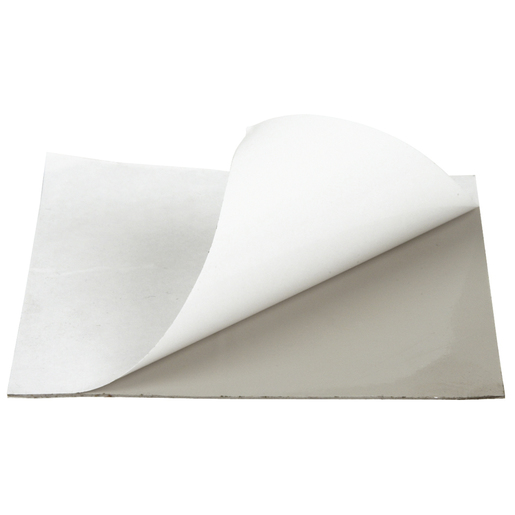
So when I decided to mount my rubidium module to the bottom of my die-cast enclosure I’ve used silicon thermal transfer tape. This material is roughly 0.5mm thick, sticky on both sides and came in a 100x100mm sheet. This is thick enough so suck up any mechanical differences between the die-cast box and rubidium enclosure ensuring the thermal tapes makes contact. This material is typically available from Mouser, Digikey and Element14; however I purchased mine from our local electronics shop Jaycar (NM2790).
Would you believe in the rush I didn’t take any photo’s of this silicon thermal transfer tape being applied, maybe on the next unit I’ll remember !
A few back of the envelope calculations suggested that this material would achieve a worst case thermal resistance of 0.085°C/W, provided the mounting screws were done up tight. This then ensures the difference in temperature between the rubidium module and enclosure could be limited to less than 3°C (worst case).
So to satisfy my own curiosity I decided to mount the rubidium module to the die-cast enclosure without a heat sink and see how hot things got. After 30 minutes of continuous operation the enclosure over the top of the physics engine was found to be the hottest, reaching +40°C in an ambient of +25°C. In a home or lab this would probably be OK, but I’m intending to take this reference with me out into the field in ambient temperatures up to +50°C.
The reference guide recommends using a heat sink with a thermal resistance better than 2.0°C/W in these situations which sounds like a good idea. So just a back of the napkin double check;
Rth(Si) = 0.09°C/W [silicon pad]
Rth(Al) = 0.008°C/W [die-cast box]
Rth(JG)= 0.25°C/W [jump grease]
Rth(HS) = 2.0°C/W [heat sink]
Tambient = +50°C [typical Australian Summer !]
Rth(total) = Rth(Si) + Rth(Al) + Rth(JG) + Rth(HS)
= 2.438°C/W
Pdiss = 28.8W (peak) 9.6W (average)
Trise = Pdiss * Rth(total)
= 28.8 * 2.438
= 67°C
Tmax = Tambient + Trise
= 50 + 67
= 117°C
OK so this will just scrape in under the typical +125°C limit for silicon devices within this rubidium module. Ditto on the capacitors.
Placing thermal paste between the heat sink and enclosure will also ensure the thermal dissipation is kept low. I prefer to call thermal paste jump grease. Since from the moment you open the tin it will somehow jump on to your elbow and then get everywhere. It’s tricky stuff to master.
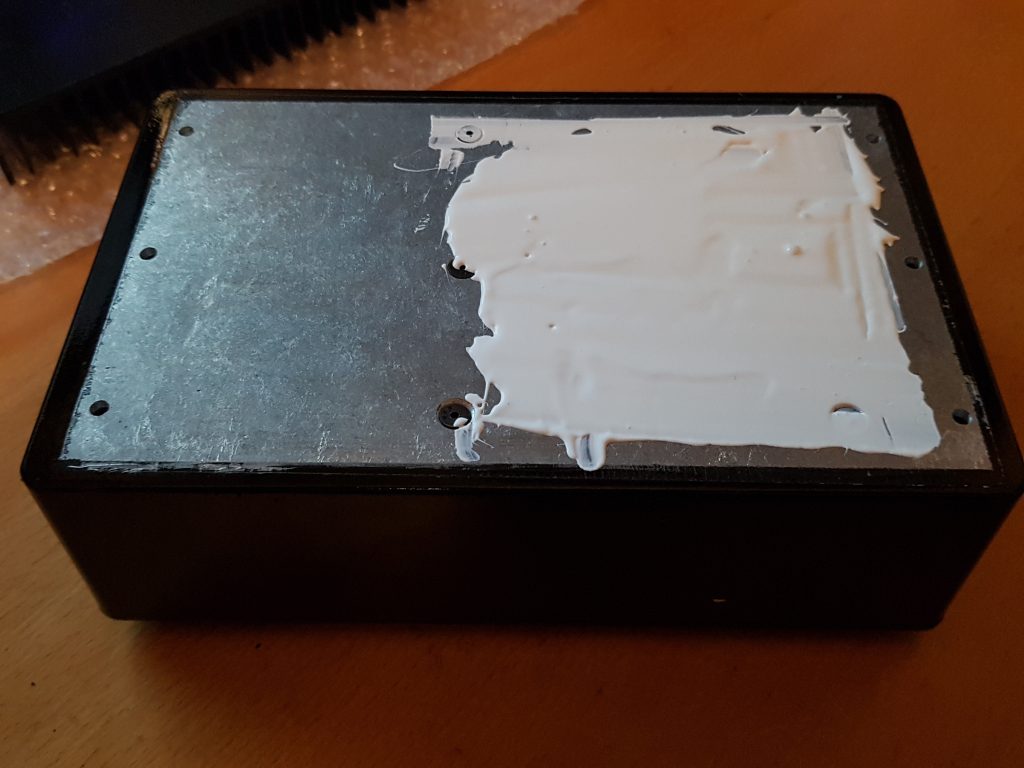
I didn’t see any point placing this grease towards the bottom of the box, since the majority of the heat comes from under the physics engine. Once this was done then the heat sink was married up to the die-case enclosure, it’s a good sign when you can see the paste squeeze out from under the heat sink slightly.

This then just requires a bit more cleanup with Turpentine, the odourless stuff is best ! Just watch this stuff, since it has a habit of squeezing out for a while if applied too thick.