The Efratom LPRO-101 has a Built in Test Equipment (BITE) signal available on Pin 6. This pin is connected to the 5V logic within the module. When the BITE signal goes LOW (0V) then the physics engine has achieved lock within roughly +/-5×10-8 of it’s absolute frequency. Thankfully it can do this within 3-4 minutes of operation.
When I’m out in the field it is certainly useful to know what the reference is doing or if something has gone wrong without having to pull it apart and get out a multimeter. So on the front panel I’ve placed two LEDs one for power and the second to show lock.
The lock signal will be nothing more than the BITE signal inverted, which can be done with one transistor. I’ve seen some quite elaborate two and three transistor circuits, but we only really need one. The circuit I’ve draw below is straight out of my engineering log book, it’s so simple I couldn’t be bothered firing up Altium to draw it;
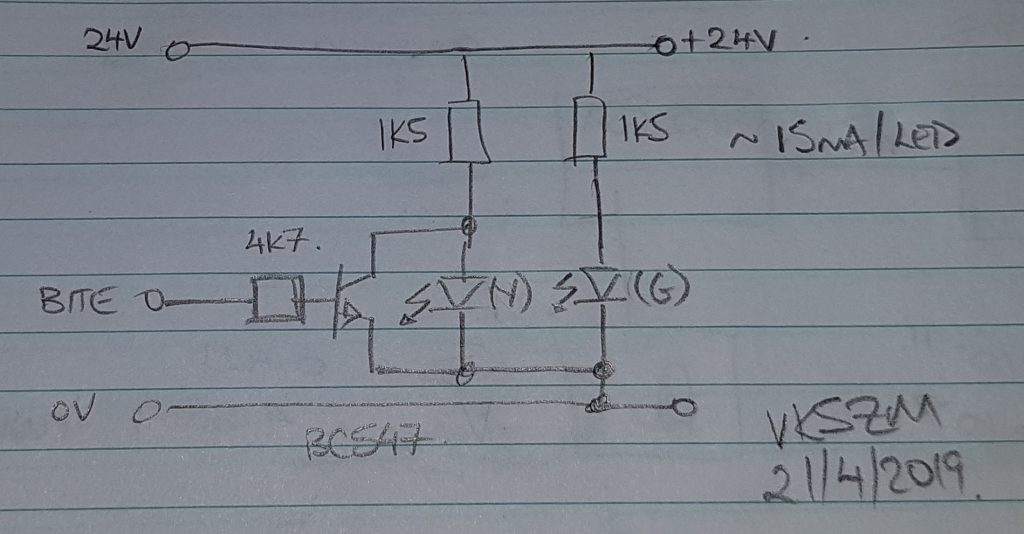
Basically we use one transistor to shunt the LED so that it is OFF while the BITE signal is HIGH. There is no rocket science here. With the heaters in the reference drawing 1.2A at startup throwing an additional 15mA through a transistor until it’s locked should be no big deal. The entire current drawn is approx 30mA, they are certainly bright enough in daylight, they might require turning down after using this at night, time will tell.

The circuit above is so simple I built it dead bug style on a piece of vero board. I did this so I could simply use double sided tape to hold it to the box and not short anything out.
One minor annoyance I’ve found is at the time power is applied the BITE output remains LOW for half a second or more before it goes HIGH. This means that the locked LED will light momentarily, then go out for 3-4 minutes as the reference warms before it lights again. The video below shows what I mean, for such a simple circuit I’m happy to put up with this feature;
You can hear the first click of the power supply, the Locked LED will light and go back out again. This was done when the reference was already warm so it takes less than 20s to regain lock again.
Anyway I’m certainly pleased with the simplicity. However now I’ve got ideas to use a micro a DAC and give this thing some intelligence. More notes in the log book for when I find time to come back to this again, for now it’s time to get out in the field and use it in anger !